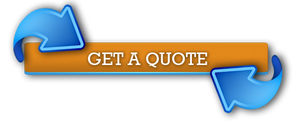
Laser Cutting Process
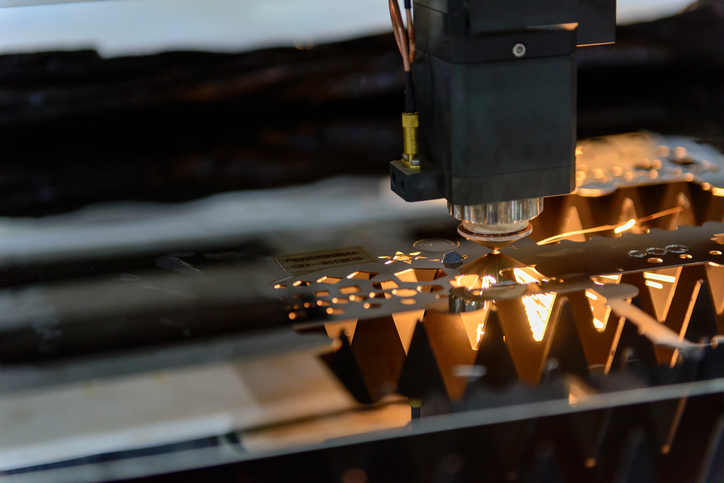
The laser cutting technology utilizes laser beams whose intensities vary to cut different materials. There are various reasons as to why laser cutting is preferred over the other techniques like plasma cutting. Laser cutters have the ability to offer unprecedented levels of machining, especially in micromachining applications.
This medium of cutting comes with so many benefits to the user. With a small or negligible heat affected zone, it results in minimal distortion parts. Since there is minimal part distortion, there is a better overall finish quality when you compare to the other methods of cutting. This drastically reduces the need for secondary finishing.
It is among the most preferred methods for intricate cutting of parts. The cutting methods produce narrow kerf widths. You can custom-build advanced laser systems for specialized tasks. With customization, the machines will have a high level of repeatability.
The laser cutting technique is CNC controlled. Therefore, close testing of parts makes sure that there is minimal wastage. The less wastage of materials translates into higher savings. The laser-cutting process is more precise and much faster than the other forms of cutting. Therefore, when it comes to attaining the exact dimensions and tolerances on high precision, delicate, thin, and small parts, the most recommended option is laser cutting.
What to Expect from Laser Cutting Services?
When you engage the services of a contract manufacturer to offer laser enabled cutting, it comes with so many benefits. First, it brings flexibility to your operations and saves you a huge amount of capital investment. You will also save yourself the training and time-consuming training processes. Laser contract manufacturers are specialized experts in a narrow field and already have the required capital investments.
Laser cutting is possible for applications like cardiovascular implants, orthopedic and dental, stents, medical devices, surgical tools, and any precision metal cutting. Contract Manufacturing Specialists of Michigan use their advanced laser cutting tools to cut an array of designs. Some of the metals that laser machines cut include aluminum, brass, copper, steel, titanium, tungsten, nickel, superalloys, and Nitinol. To add on these metals that are commonly used, other materials for laser curing are rubber, fused quartz, ceramics, wood, and plastics.
The other common application of laser-enabled cutting is the precision tube cutting. The process is achieved by introducing a fourth axis that rotates the tube during the cutting process. The laser can cut tubes whose diameter ranges from 0.0125 to 6 inches. The tubes can be used for implants or medical devices. With laser cutting, you can attain the dimensions of both small and large parts. Therefore, laser cutting works on a variety of materials with a high level of precision. However, as a company, we specialize in metal laser cutting alone.
The laser cutting technique uses small mirrors to guide light from the machine to a specific location on the material. The cutting material bases are manufactured from a honeycomb material to allow the laser light to pass through them. You have to replace this periodically.
Laser cutters are very different from the mechanical traditional cutters. The laser does not make any physical contact with the material that you are cutting hence there are minimal chances of contaminating the material. Laser cutters also have a high level of precision than the one you get on mechanical means. The quiet process is the other advantage of laser cutting over the traditional process. Because safety is crucial in laser cutting, most cutters are enclosed to avoid accidents.
The CO2 laser is the most common type of laser machine that is available in the market. It has become the industry standard because of its efficiency, cost, and power available. The finish of the CO2 laser cutter is better than other processes like plasma or oxy. Proper use of gas pressures, pulse settings, feed speeds, and efficient nozzles product good square parts that have very smooth finishes. For most of the applications, you only need minimal post finishing. However, the CO2 laser cutting does not replicate machined finishes. Typically, the parts have an affected heat zone but it is smaller when you compare with the traditional processes. There are minimal heat distortions which are among the top benefits of laser cutting.
You can use CO2 laser in all applications where more conventional processes like plasma and oxy apply. However, CO2 laser goes ahead to cut a wide range of materials like wood and plastics. You can mount CO2 laser cutter on different motion systems from gantry systems to cut large plates to small desktop units for handling smaller tasks. The application of C2 laser cutting includes cutting thin sheet metals, drilling or cutting holes in steel parts, and profiling sheet metals among others.
The laser cutting technology is highly potent and you can use it in cutting resistant and tough materials like copper alloys, aluminum, stainless steel, etc. the industry of metal fabrication uses technology extensively in the production and cutting of sheet metal. The cutting technology enhances productivity speed, decreases the cost of productions, and improves the cutting quality. Laser cutting relies on the emission of a light beam via a stimulation process that users the laser cutter device. The industry utilizes a broad range of lasers basing on the process it utilizes to emit light beams. As we said, the most common one was CO2. This gas laser is expansively used for welding across the industry. The technology can produce maximum energy of 100KW at 9.6um and 10.6um and cuts 20-30 meters of materials whose thickness is 1mm in a minute.
During cutting, the produced energy is aimed at smaller portions of the material to be cut to produce a hole. You move the light beam along the line to complete the cut. When the materials are handy enough, you move it across the point where a steady light stream is projected. The point where the powerful light beam strikes the sheet metal quickly heats up., melts, and then evaporates. The amount of energy that the laser delivers depends on the type of material that you are cutting. It will produce a lesser amount of energy if you are cutting thin materials. On average, however, 1 to 1.5KW of energy is sufficient to cut almost all types of materials. However, steel and other resistant materials need 2KW or more of energy.
Some of the advantages of the laser cutting process include affordability, cutting speed, and accuracy of the job that you are doing. With these advantages, laser cutting becomes the most popular cutting technology in the industry of sheet metal fabrication. However, like any other technique, laser cutting also has its own set of disadvantages. For example, laser machines need high voltages to operate. In addition to the high consumption of power, lasers also expose you to the risk of electrocution or burns. However, the benefits of using a laser in cutting sheet metal outweigh the drawbacks of the technology. It is a good way to improve the precision and speed of your work.
A few years ago, most of the old-fashioned metal fabrication companies were using other technologies to cut sheet metal. However, most of there are now aware of the revolutionary way of doing things hence turning to laser cutting. Surprisingly, we still have people who believe that the laser cutting process is the next generation of technology which is still in the experimental stages. The technology is widely popular among several companies across the industry that integrate seamlessly with various processes like CSM/CAD and help then to work with the automated processes. The best thing is the end products of the laser cutting process that are quite perfect. If you are not yet taking advantage of the laser cutting process, it is wise to start using it now.
Given the quality of staff and equipment that we have, you can be sure of getting the best rates from our brand. To benefit from our services, feel free to call us today. We have a team that is ready to give you the best services all the time.
Our core offerings and services at Contract Manufacturing Specialists of Michigan includes, but is not limited to, the following below:
We service multiple cities throughout the state of Michigan. We provide all the services listed above, and much more in every city throughout Michigan.
If you don’t see your city listed or a specific service listed, don’t worry. All you have to do is contact us by either giving us a call or filling out our online contact form. Then we’ll discover what are some of the top solutions for you, your business, and executing a solid solution.